Komax Kappa 330 Cut & Strip
The Kappa 330 convinces with its wide processing spectrum. It is available as Single Head or Dual Head, whereby the Single Head can be converted to a Dual Head. Two blade variants are available simultaneously as Dual Heads. With optional slitting unit, inner conductor and ribbon cable processing, the Kappa 330 is perfect for customers who want to process a wide range of cables.
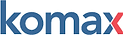
Single head with versatile processing range
-
Cutting to length and stripping from 0.22 – 35 mm² (AWG 24 – 2) cables.
-
Processing of cable cross-sections up to 35 mm², multipole conductors up to Ø 16 mm (0.63 in.). Even short cables or ribbon cables up to 40 mm (1.6 in.) wide can be processed without any problems.
-
Innovative sensor technology as set-up aid and process monitoring.
Dual head for even more productivity
-
The dual-head version of the Kappa 330 has a double-blade stripping unit.
-
With the double-blade stripping unit, various special knives can be used simultaneously for cutting and stripping.
-
Particularly challenging wires can be processed quickly and precisely using special blades.
-
Together with further options, the dual-head Kappa 330 offers three processing steps in one pass.
Optional separating unit
-
Several (also twisted) inner conductors can be separated quickly and gently - without loss of quality.
-
Using the patented Komax roller system, the wires are pressed apart in a particularly gentle way.
-
The forward and reverse function of the rolls allow even short wires to be processed with ease.
Optional slitting unit
-
Programmable depth adjustment
-
Fully controllable via touch operation
-
High benefit
Wide range of applications
The Kappa product family stands out thanks to its extremely broad processing range. Its intuitive and simple operation and controls allow you to easily set up even difficult-to-process materials, with extremely fast tool-free changeover to new types of wires.
Fast, simple operation
The intuitive TopTouch operating software guides the user through the process logically. During production, operators have maximum transparency thanks to simple adjustment settings for important parameters. This makes the Kappa machines especially intuitive and safe to operate.
Automatic diameter detection
The sensor-enabled wire diameter and cross-section detection makes it possible to set up and parameterize new wire materials at the push of a button. The unique, tool-free measuring principle reduces time-consuming setup to a minimum, while cut losses are also minimized thanks to the optical wire monitoring. The laser sensor continuously checks and immediately detects wire ends and stripping errors during production.
TopWin Kappa – enhanced capabilities
The TopWin Kappa operating software expands the capabilities and functionality of Kappa machines via a PC user interface. Inkjet printing in multiple positions, mirror printing and double-sided labels can be controlled, including everything from pre-printed wires to logo markings and more.
Intelligent economical production
Products with the same wire are produced without cuts and therefore more economically with the help of job lists. Sequence production and part list processing are also possible. Products may be loaded directly into the job list, even while production is running. Changeover times are minimized thanks to automatic sorting of the different products.
Different types of production as required
Depending on the production process, part lists or sequences can be produced as multi-lead sets or as cable harnesses. In addition, TopWin makes it possible to verify materials, detect material changes or print commercial documents.
Perfectly networked
TopWin Kappa can be easily integrated into networks via the WPCS interface, including, for example, existing user networks. The production-control room software also enables centralized data management, production control and production monitoring.
Applications:

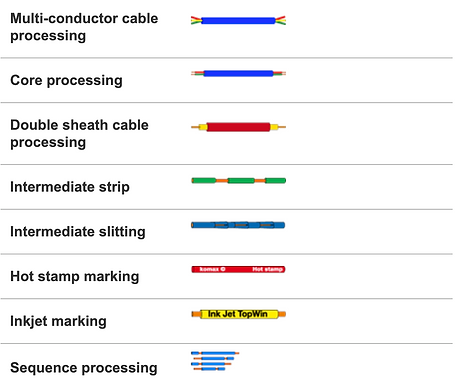
Technical Data:


